Case Study: TT Optimal develop direct keg filler solution for Pilot Brewery
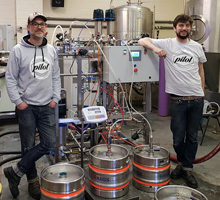
Until recently the majority of smaller craft brewers have sold their beer predominantly in casks. Beer in cask has is very much seen as the traditional method getting beer to market and has the smallest requirement in terms of capital equipment.
In recent years kegs have become available to ‘hire’ on a per use basis from companies such as E Kegs and Kegstar. While not perceived as traditional, kegs do offer several advantages to breweries i.e. longer product life, consistent CO2 levels, being significant advantages. Another advantage to the brewer is that installing a tap at a bar brings not only brand visibility, but a commitment from a bar to sell that product and with that a level of certainty for the brewer for beer sales.
The transition from cask to keg does not mean that the beer has to lose any of its character, yes mass market beers are filled bright, pasteurised and often highly carbonated into Keg. But it doesn’t have to be like that. Beer can be filled into kegs unfiltered and hazy and with a thoughtful level of CO2. But to achieve high standards the hygiene and process is critical.
Moving from cask to keg has traditionally required conditioning tanks which allow the beer to be conditioned and carbonated before going to cask. This can be a major stumbling block given the costs and space required for equipment. However a solution currently being used by Pilot Beer Ltd in Leith shows what is possible with current technologies available in process equipment.
Pilot asked TTO to design and build a keg filling system that would fill beer into kegs directly from their fermentors. A skid mounted unit was built and tested and is now in operation in their Leith Brewery. The unit connects directly to a fermentor and the chilled beer is strained for particulates, filtered (or not), carbonated by a mass-stream carbonator, and filled into kegs. The system uses bottled CO2 and CO2 consumption is minimised by recovery of CO2 displaced during filling. The system can process and fill up to 1000 litres per hour.
Matt Johnson of Pilot said “our initial concerns about the complexity of the unit are behind us now, in operation it is very simple. However cleaning and preparation for a run are critical to product life and quality. The system has made a huge difference to the capacity of our brewery as we only had one conditioning tank, now we fill directly from fermentor.”
With the first unit installed and working TTO is working on ways to make this technology easier to use and enable more small brewers to make the move to kegging and the advantages of using this package.
For more information: